Several decades have passed since dental impression disinfection has been integrated in modern dentistry as a way to prevent cross-infection to the dental team [1–8]. Various studies have shown that handling contaminated dental impressions can lead to infections, as well as the stone casts that are poured from them [7,9,10]. Although most of the microorganisms adhered to the dental impression surfaces are removed by rinsing under running tap water, a high percentage still remains [11,12].
Since conventional sterilization methods, such as dry heat sterilization, cannot be used for eliminating potential pathogen microorganisms that are present on the dental impression surface [13–15], liquid chemical immersion disinfection is currently the most widely accepted method [1,16–20]. Current commercially available immersion disinfection solutions contain sodium hypochlorite (0.525%), quaternary ammonium compounds, glutaraldehyde, phenols and iodophors in various concentrations and immersion times [1,2,10,16,18,21]. Apart from immersion disinfection, alternative methods have been suggested, such as spray disinfection [19], steam autoclave [15], ozone [22], microwave [23], ultraviolet light [24], etc.
The action of environment friendly ozone as an oxidizing compound is well known since the 19th century [25,26] and is being used in a wide range of applications as a disinfecting agent [27]. The disinfection activity of ozone is due to its ability to attack the cell membrane and intracellular enzymes of microorganisms, as well as the viral capsids and DNA [22]. Ozone is produced from ozone generators, in-situ, because it is an unstable compound which possesses a 40 minute half-life at 20oC [28]. Ozone generators make use of either “corona discharge” technology, ultraviolet light or electrolysis [29,30].
Impression materials possess physical and chemical properties that are prone to even minor changes after chemical or physical disinfection methods [24]. The surface of these materials is important to remain unaffected after the disinfection procedure in order to obtain high precision reproduction casts. It is not clear if disinfection of dental impressions alters their surface because of the diversity of the results in the literature. Several studies have been conducted focusing on the surface degradation of impression materials after immersion disinfection [1,21,31]. The usual method of measuring the possible surface degradation of these materials is profilometry, although other methods have also been used, namely optical microscopy [31–34]. Few Scanning Electronic Microscopy (SEM) studies have been conducted regarding the effects of immersion disinfection on elastomeric impression materials [1,21].
Surface degradation is usually expressed by surface roughness which is a result of the polymer chain scission process that takes place during chemical treatment [35]. It has also been shown that chemically [36,37] or ozone [38–46] treated polydimethylsiloxane elastomers, show alterations on their surface. Such alterations can be expressed by wrinkles like those found in systems that are constituted of thin metal films adhered on polydimethylsiloxane which undergo temperature changes or mechanical deformation, such as elastic buckling [47,48]. This behaviour is also encountered in systems where non-elastic films are adhered on elastic substrates [49,50].
The aim of this study was to qualitatively examine with SEM, the possible surface degradation of dental impression materials caused by immersion and environment friendly ozone disinfection. The null hypothesis was that both immersion and ozone disinfection would not alter the surface of the dental impression materials.
Materials and Methods
This in-vitro study was performed at the National and Kapodistrian University of Athens, School of Health Sciences, Faculty of Pharmacy, Department of Pharmaceutical Technology and the Technological Educational Institute of Athens, Faculty of Health and Caring Professions, Department of Dental Technology (study period 2010–2013).
Impression Materials: Four impression materials were used in this study, of which two were vinyl polysiloxane silicones (Aquasil Ultra LV-Regular Set, Dentsply International Inc., York, Pennsylvania, USA and Express-Regular Set, 3M ESPE, St. Paul, Minnesota, USA), one polyether (Impregum Garant L Duosoft-Regular Set, 3M ESPE, St. Paul, Minnesota, USA) and one vinyl polyether silicone (Exalence-Regular Set, GC Co., Tokyo, Japan). All impression materials used were in the dual cartridge form and dispensed using the special dispenser gun (Dispenser gun type 2, Voco GmbH, Cuxhaven, Germany).
Specimen Fabrication: A total of 32 elastomer specimens were produced, eight from each impression material (eight groups of four different impression materials). A small quantity of elastomeric impression material was placed in the center of a microscope slide (Microscope slides, Waldemar Knittel Glasbearbeitungs GmbH, Braunschweig, Germany), while two small, 1mm diameter, orthodontic wire pieces were placed on the slide’s surface bilaterally and a new microscope slide was pressed on top of the impression material until it came in contact with the wires which acted as stoppers [Table/Fig-1].
The impression material polymerized in between the microscope slides.
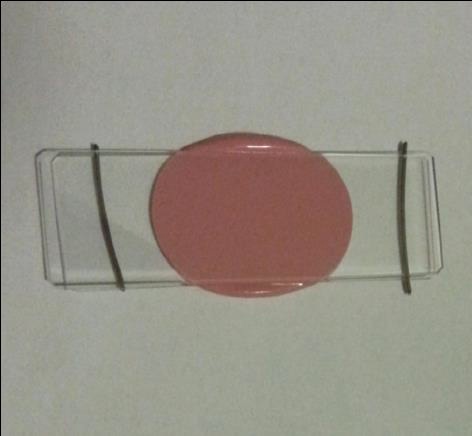
The microscope slides were divided after the polymerization time (10 more minutes were added to the manufacturer polymerization time to compensate for ambient air polymerization). The polymerized specimen was placed in a new petri dish, paying attention on the surface of the specimen not to come in contact with any object.
Disinfection Methods: The disinfection methods examined were that of ozone disinfection via a prototype ozone disinfection device for dental impression materials (Group G and H), sodium hypochlorite immersion disinfection (Klinex, Unilever Hellas, Athens, Greece) (Group C and D) and benzalkonium chloride immersion disinfection (Prosept® Impression, OCC, Fehraltorf, Switzerland) (Group E and F). Some specimens also served as controls (Group A) and some were wash bottle rinsed via tap water for 10 seconds (Group B).
Ozone Disinfection Device: A prototype ozone disinfection device for dental impression materials was constructed (Greek patent office registration number: 20110100194/2013). Ozone is generated by a corona discharge ozone generator (OZV-4, Ozone Solutions Inc., Hull, Iowa, USA) from ambient air which dries through an air dryer (MAG-600, Ozonesolutions Inc., Hull, Iowa, USA). It is directed through teflon pipework into an 18x14x9cm (LxWxH) sealed disinfection chamber and is removed from the chamber for destruction through a manganese dioxide-copper oxide catalyst (ODS-1P, Ozonesolutions Inc., Hull, Iowa, USA). Ozone flow is controlled by a high precision 0–20 L/min flow meter (EK-4BR, Kytola Instruments Oy, Muurame, Finland) via an adjustable flow valve.
The disinfection is conducted by constant flow of ozone with a flow rate of 4L/min and ozone production of 2.61g/h. During the experimental procedure, 2 minutes are added to the ozone exposure intervals aiming in reaching the ozone concentration upper threshold at the onset of the real exposure time. The completion of the exposure time follows the disruption of ozone supply and a subsequent feed of the chamber with ambient air for 10min, at a flow rate of 4 L/min, to completely wash it out of the ozone mixture. All manipulations of the ozone disinfection device are controlled by an electronic control panel [22].
Specimen Ozone Disinfection: The specimens were placed inside the disinfection chamber of the prototype ozone disinfection device and ozone disinfected for the specified time according to [Table/Fig-2]. After completion of the disinfection cycle, the specimens were removed from the disinfection chamber and were placed in new petri dishes.
Combination of the disinfection methods and disinfection time used for the samples examined in this study.
Disinfection Method | Disinfection Time | Sample Size |
---|
Control (Group A) | - | 4 |
Rinsed samples (Group B) | - | 4 |
Sodium hypochlorite (Group C) | 10minute | 4 |
Sodium hypochlorite (Group D) | 30minute | 4 |
Benzalkonium chloride (Group E) | 2minute | 4 |
Benzalkonium chloride (Group F) | 30minute | 4 |
Ozone (Group G) | 5minute | 4 |
Ozone (Group H) | 15minute | 4 |
Specimen Immersion Disinfection: The specimens were immersed in either 0.525% sodium hypochlorite solution or 0.3% benzalkonium chloride solution for the specified time according to [Table/Fig-2]. After completion of the disinfection, the specimens were removed from the disinfection solution and were wash bottle rinsed via tap water for 10 seconds. The specimens were dried through compressed air under ultra-low pressure and placed in new petri dishes.
Specimen SEM Preparation and Examination: After specimen disinfection, a 7mm disc was removed from each of the specimens (disinfected or control) using a dental copper ring paying attention not to destruct the upper surface of the disc. The separated discs were mounted on aluminium SEM stubs with carbon conducting cement (Leit-C, Plano Gmbh, Wetzlar, Germany) and sputter-coated with gold (SC7640, Polaron, Quorum Technologies Ltd., East Sussex, UK). All specimens were examined under a JEOL SEM (JSM-5310, JEOL Ltd., Tokyo, Japan) operating at 25kV and X2000 magnification.
Results
The surface effects of immersion and ozone disinfection of the four elastomeric impression materials chosen are presented through the SEM images in [Table/Fig-3,4,5 and 6]. For the vinyl polysiloxane silicones examined (Aquasil and Express) as well as for the vinyl polyether silicone, when treated with 0.3% benzalkonium chloride for 2 minutes, the response of their surface was similar. A wavy-wrinkling surface structure was obtained which in all cases presents small wrinkling wavelength [Table/Fig-3b,4b,5b]. The polyether examined showed a wrinkling pattern in the control specimen as well as in the benzalkonium chloride treated specimen for 2 minutes [Table/Fig-6a,6b]. Similar wrinkling patterns were obtained for the ozone disinfected Aquasil specimen [Table/Fig-3c], although showing sites with intense wrinkle characteristics.
Representative SEM images of aquasil vinyl polysiloxane silicone (x2000): (a) control (no disinfection); (b) 2 minutes 0.3% benzalkonium chloride; (c) 5 minutes ozone.
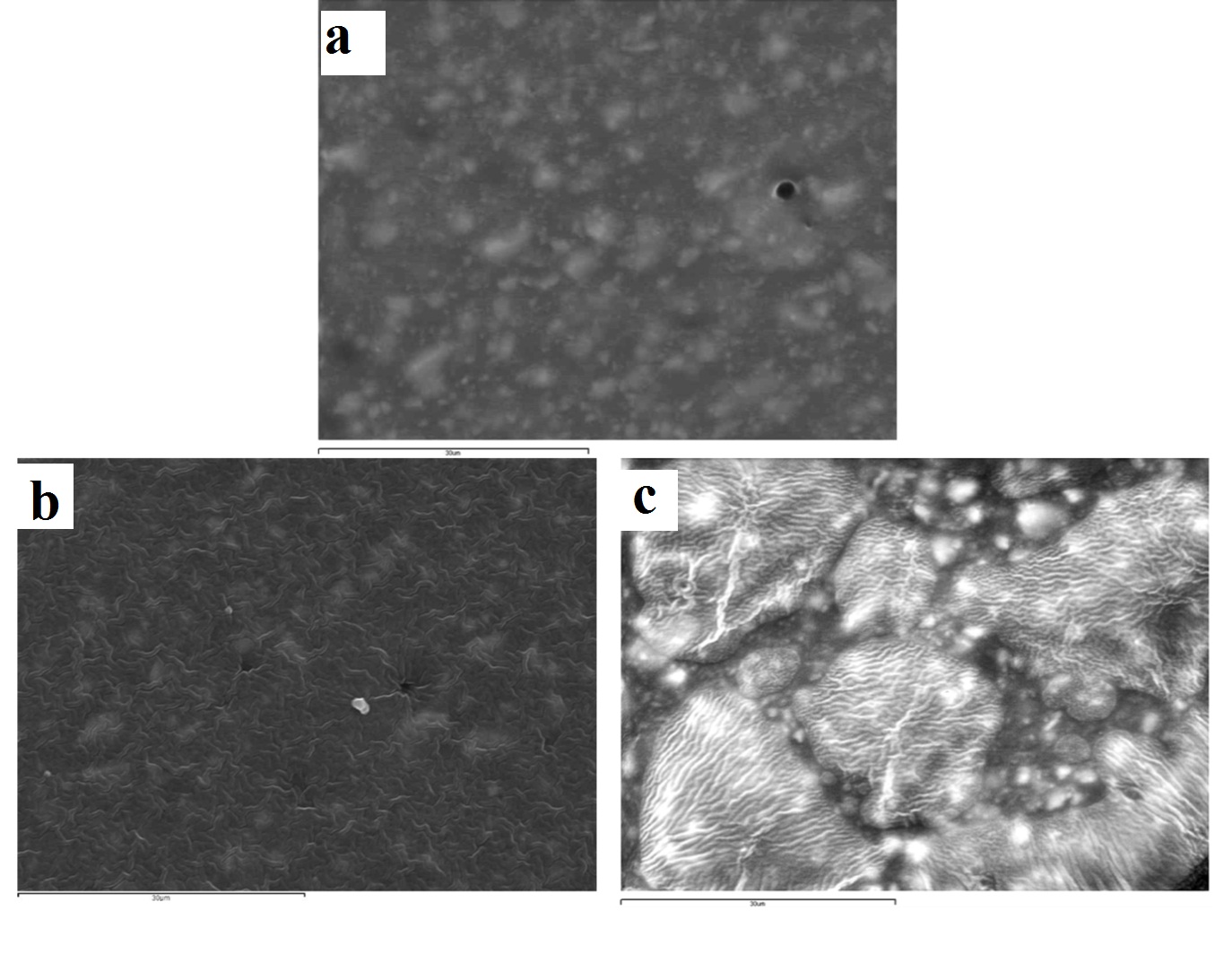
Representative SEM images of express vinyl polysiloxane silicone (x2000): (a) control (no disinfection); (b) 2 minutes 0.3% benzalkonium chloride; (c) 30 minutes 0.525% sodium hypochlorite solution.
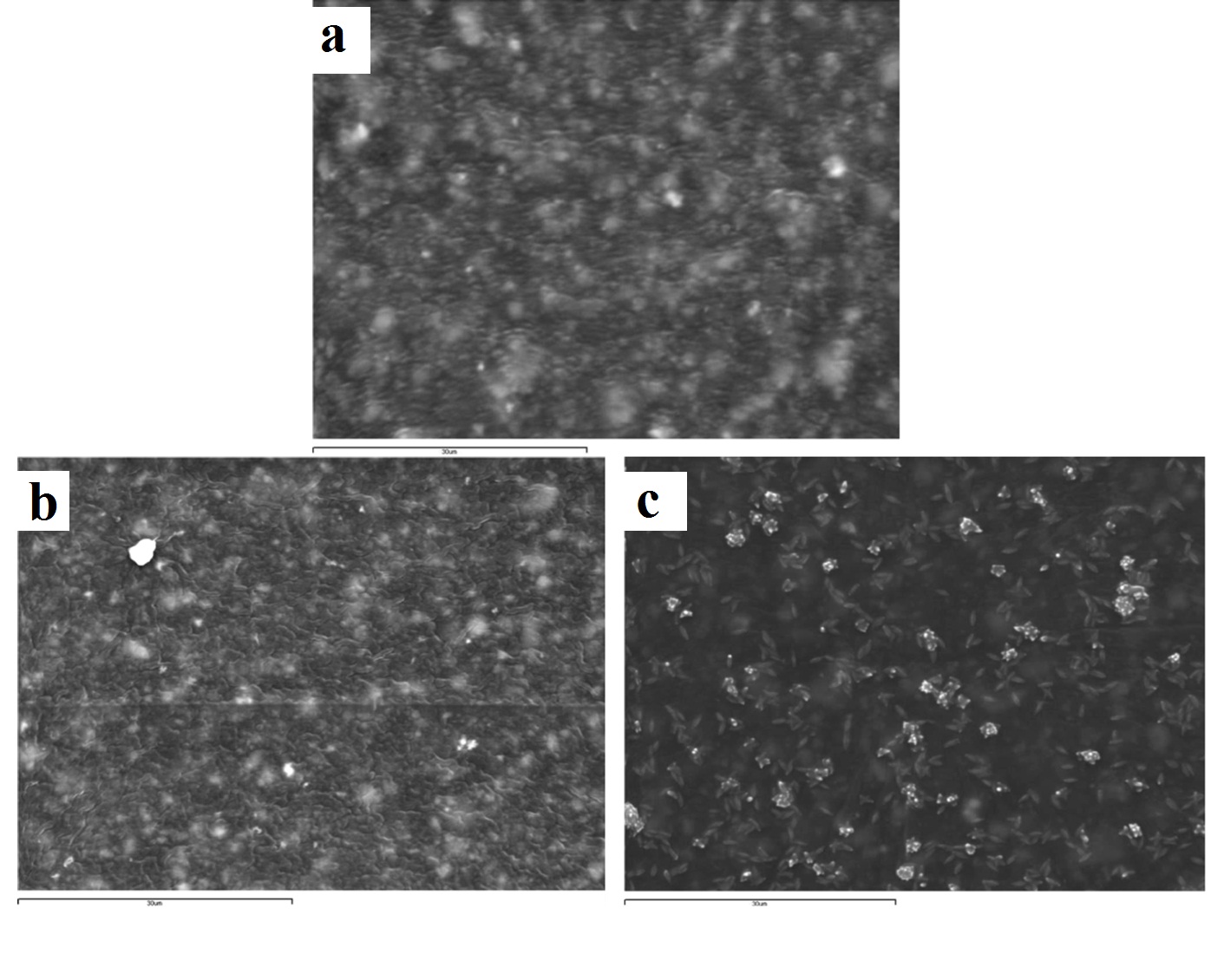
Representative SEM images of exalence vinyl polyether silicone (x2000): (a) control (no disinfection); (b) 2 minutes 0.3% benzalkonium chloride.
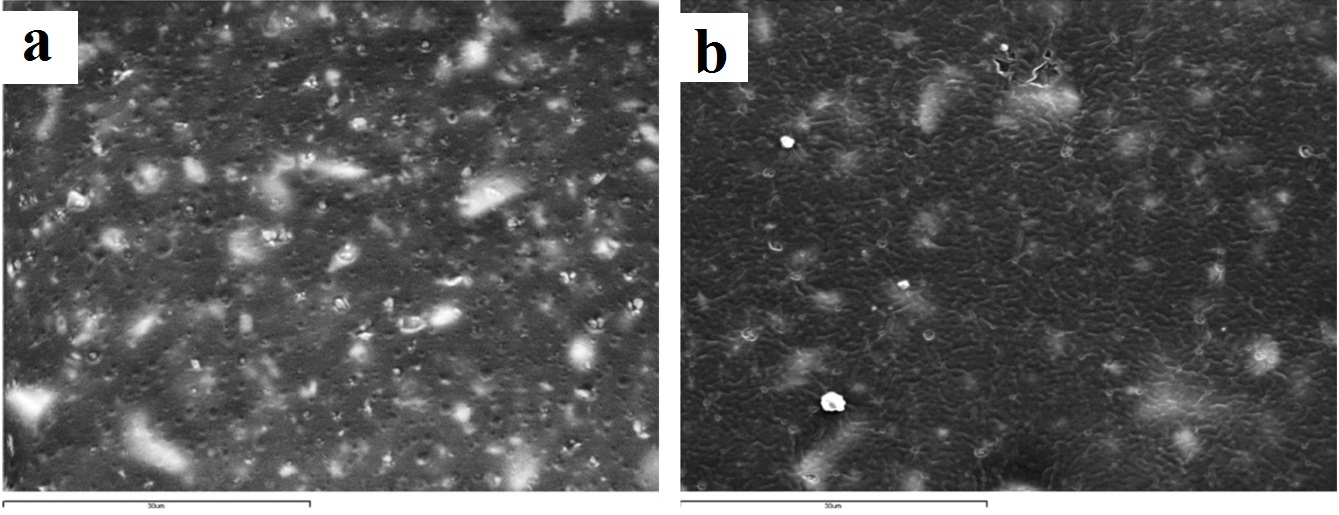
Representative SEM images of impregum polyether (x2000): (a) control (no disinfection); (b) 2 minutes 0.3% benzalkonium chloride; (c) 5 minutes ozone.
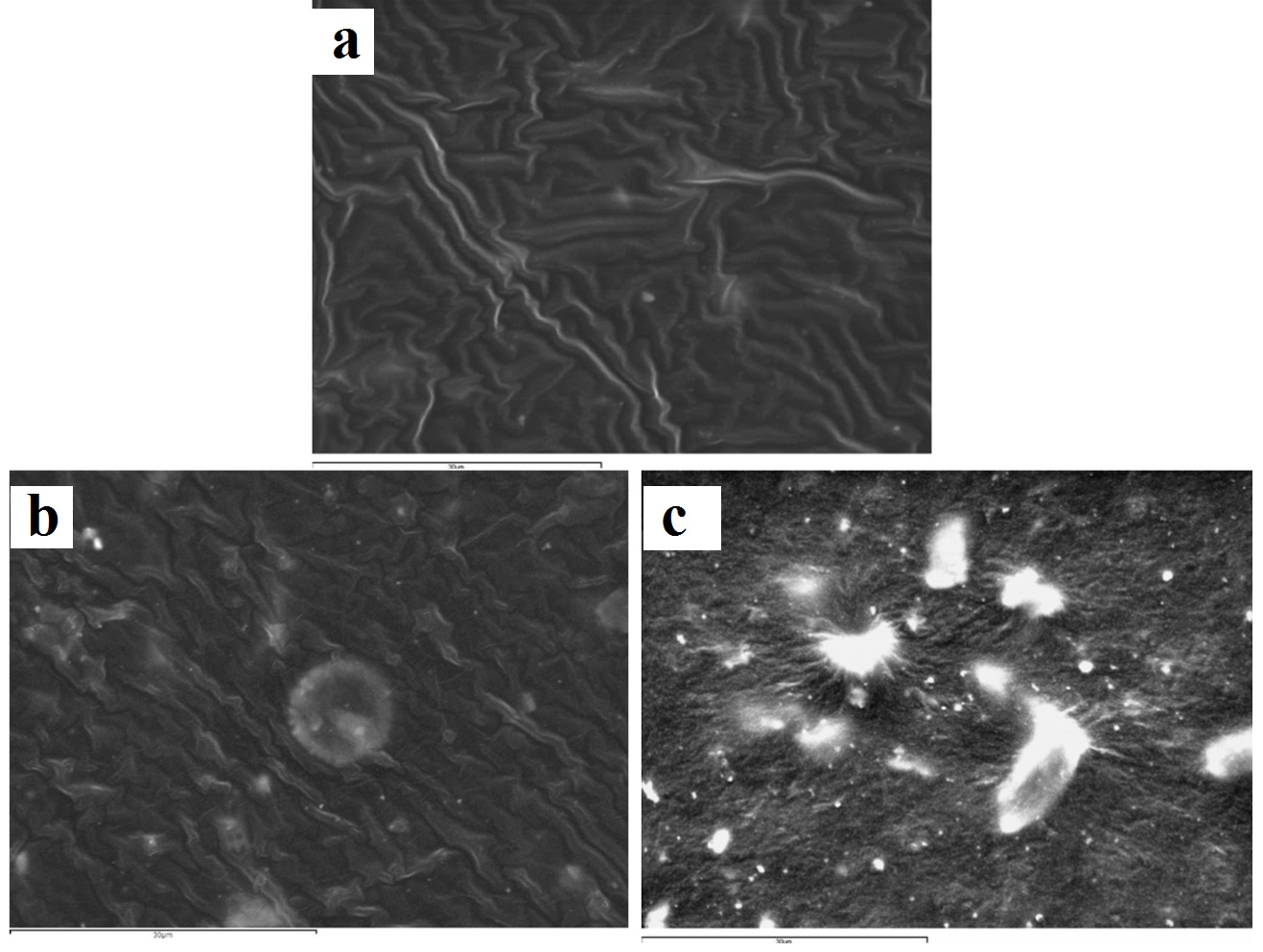
The Express vinyl polysiloxane specimen, when treated with 0.525% sodium hypochlorite for 30 minutes, showed extensive surface degradation while silicon dioxide crystals emerged from the surface of the specimen [Table/Fig-4c]. Similar behaviour was encountered in the 5 minute ozone disinfected polyether specimen [Table/Fig-6c].
Discussion
The 10 minute disinfection time for the 0.525% sodium hypo-chlorite immersion disinfection was selected according to ADA specifications [1,2,10]. The 2 minute disinfection time for the 0.3% benzalkonium chloride immersion disinfection was selected according to the recommendations by the manufacturer. The 30 minute disinfection time for both immersion disinfectants was selected for the case of extended immersion time due to factors such as impressions being forgotten immersed, which happens in daily practice. The 5 minute ozone disinfection time was selected based on previous work [22] which showed efficient disinfection results. The 15 minute ozone disinfection time was incorporated in case further microbiology experiments (regarding different bacteria or viruses) show that more time is needed for disinfection.
Although the surface roughness of disinfected impression materials has been well documented, the resultant impression material surfaces have not been extensively qualitatively illustrated via SEM [31,32,34]. The Express vinyl polysiloxane specimen disinfected with 0.525% sodium hypochlorite showed extensive surface degradation leading to emergence of silica crystals on the surface. It has been shown that polymers degrade through polymer chain scission process during which oligomers and finally monomers are formed and leave the polymer [35]. In this way, silica crystals emerge on the polymer’s surface, with one portion being embedded inside and the other outside of the polymer [Table/Fig-4c]. This finding is in contrast with other studies, where no surface change occurred on vinyl polysiloxane specimens that had been sodium hypochlorite disinfected at the same concentration and disinfection time [1,21].
The wavy-wrinkling surface encountered on all benzalkonium chloride disinfected specimens [Table/Fig-3b,4b,5b,6b] is of great importance, since this active ingredient belongs to the quaternary ammonium compounds family which serves as one of the most widely used impression disinfectants in modern dentistry. Several studies have been conducted focusing on wrinkle surface formation of elastomeric vinyl polysiloxane substrates that are used in a wide range of applications, such as tissue engineering and latest technology electronic devices [36,49,51]. However, in the available literature, there is no study that emphasizes on wrinkle surface formation of disinfected dental impression materials. It has been shown that when thin metal films (in the order of 50nm in thickness) are deposited onto vinyl polysiloxane substrates which are then subjected to temperature changes, they obtain highly ordered patterns with distinctive features, by elastic buckling [47,48]. This particular behaviour is broadened to systems that consist of thin–rigid membranes adhered onto soft elastic substrates [49,50]. Wrinkle formation is related to contraction and expansion of the elastomeric substrate during which, compressive stresses are induced on the non-elastic film that covers the elastomeric substrate. The non-elastic film obtains this wrinkling surface, presenting a wavelength in the order of few to hundreds of micrometers, in order to relieve the rigid film from the compressive stresses induced. The wavelength and orientation of the wrinkles are fully controllable [37,47]. Wrinkling surface formation of vinyl polysiloxane silicones can also appear after contact with chemical solutions, such as sulfuric acid/nitric acid [36,37]. Due to the oxidative action of acids, the vinyl polysiloxane surface exhibits fracture of its methyl groups from the polymer chain leading to silanol group formations. These silanol groups undergo self-condensation reactions, producing siloxane bonds resulting in cross-linking of the polymer chains on the surface of the elastomer. Thus, the vinyl polysiloxane surface acquires a stiffer, non-elastic nature, similar to silica, than the non-oxidative elastic substrate. In this way, a rigid surface film is generated on top of the elastic substrate of the vinyl polysiloxane. The mismatched Young’s modulus of the two layers leads to generation of compressive stresses which are relieved by wrinkle formation on the surface. Through this mechanism, in the benzalkonium chloride disinfection case, the non-elastic polymer film that is formed due to oxidation of the surface takes the form of a wavy-wrinkling surface due to internal stress release [36,37].
A similar wavy-wrinkling surface was encountered in the 5 minute ozone disinfected Aquasil vinyl polysiloxane specimen. This behaviour is confirmed by other studies and is strictly related to the vinyl polysiloxane surface oxidation by ozone and the subsequent formation of a stiff silicon dioxide film [38–43], in a similar way to that described in the benzalkonium chloride chemical disinfection. More specifically, during the elastomer surface oxidation by ozone, the methyl groups that are present on the surface are fractured from the polymer chain [42–44] and silanol groups are formed [41,44–46]. These silanol groups produce siloxane bonds resulting in cross-linking of the polymer chains on the surface of the elastomer. As for the ozone disinfected polyether specimen that showed extensive degradation [Table/Fig-6c], this might be due to the oxidative action of ozone which cleaves the cross-links and the methyl groups of the polymer. The oligomers and monomers are removed from the surface and silica crystals emerge.
In the polyether control specimen case [Table/Fig-6a], a wrinkling surface was observed in opposition to the other three control specimens. The polymerization shrinkage which takes place [52] is likely to induce internal stresses close to the surface of the specimen which came into contact with the microscope slide. This is confirmed from other studies which show that when polymers are subjected to thin-film specimen construction, internal stresses are induced in the polymer chains [53]. In addition, great distortion was instantly encountered by the polyether specimens during removal from the microscope slides, on which were strongly adhered in contrast to the other elastomer specimens. This instant distortion in conjunction with the induced internal stresses has possibly been expressed on the gold sputter-coated rigid surface of the control specimen with the distinctive wrinkle formation. This finding was encountered only in the polyether control specimen, meaning that the mechanism explained concerns only this type of elastomeric impression materials and not the silicone controls [Table/Fig-3a,4a,5a].
In order not to be misled to wrong conclusions regarding the immersion disinfection of the specimens, another group of four specimens was incorporated in the study which was not disinfected but instead, wash bottle rinsed via tap water. This helped to exclude false conclusions that could possibly be linked to the wash bottle rinse that followed the immersion disinfected specimens. These four SEM representative images are not shown in this study, as no major effects were observed on their surface. Likewise, SEM images (17 images) of the rest of the specimens which did not show any notable surface alterations were not incorporated in the present paper.
Comparing all disinfection methods in conjunction with their effects on each impression material’s surface, similar alterations were observed on almost all specimens, which confirms the null hypothesis that both immersion and ozone disinfection would not alter the surface of the dental impression materials. This is confirmed as the immersion disinfection active ingredients used in the present study (sodium hypochlorite and quaternary ammonium compounds) are two of the most widely used in modern dentistry. Ozone, as a new, environment friendly, alternative dental impression disinfectant seems to be highly promising, designating a time saving method, without the need of consumable materials, which can be applied in every dental office since it requires limited space.
Limitation
In order to further assess these dental impression materials dis-infection methods, other physical mechanical changes may have to be additionally investigated, such as dimensional stability and surface roughness quantification
Conclusion
This study revealed that although dental impression immersion disinfection does not affect macroscopically the materials’ surface, several reactions of these disinfectants lead to severe alterations on microscopic scale. The proposed alternative and environment friendly dental impression disinfectant (ozone) shows similar impression surface alterations with those of the immersion disinfectants examined, providing non-inferior results as compared to immersion disinfection and superiority as to environmental protection. Clinically, the use of a dental impression ozone disinfection device provides a new method which needs no consumables, is time saving, requires limited space in the dental office and is environment friendly, minimizing environmental hazard through liquid waste generation. In addition, it does not show any surface differences when compared with the everyday-use disinfectants, an exceptionally important factor that leads to highly accurate prosthetic restorations.